Eva Pack Machinery is leading manufacturer company of high quality products. business services such as Liquid Filling Line, Automatic Capping Machine, Powder Filling Machine, Servo Based Liquid Filling Machine All Type Of Machinery,
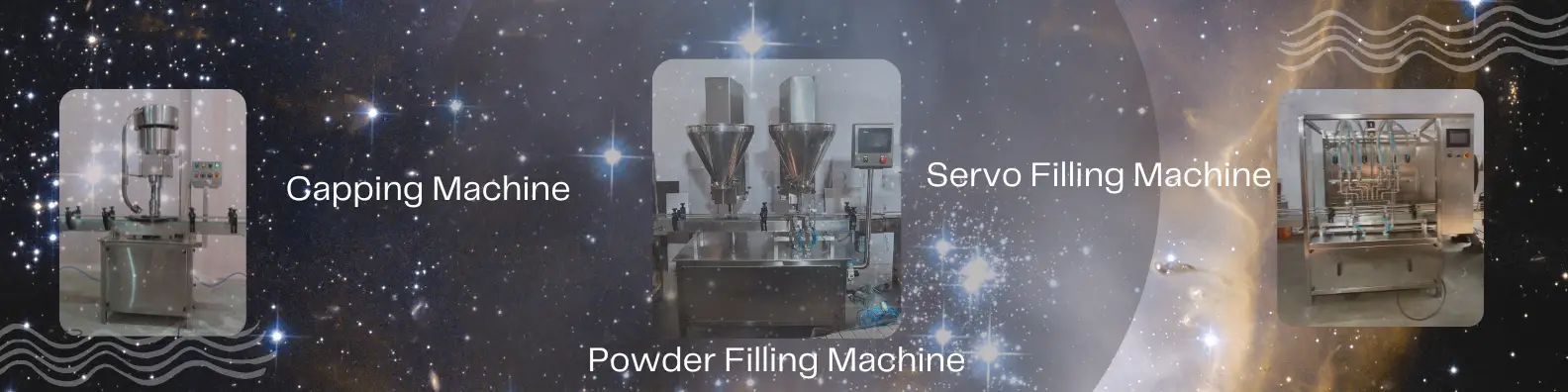
Industries
Pharma Industries, Food Industries, Ayurvedic Industries, Oil Industries, Beverages Industries, Pesticide Industries,
OUR PRODUCT:
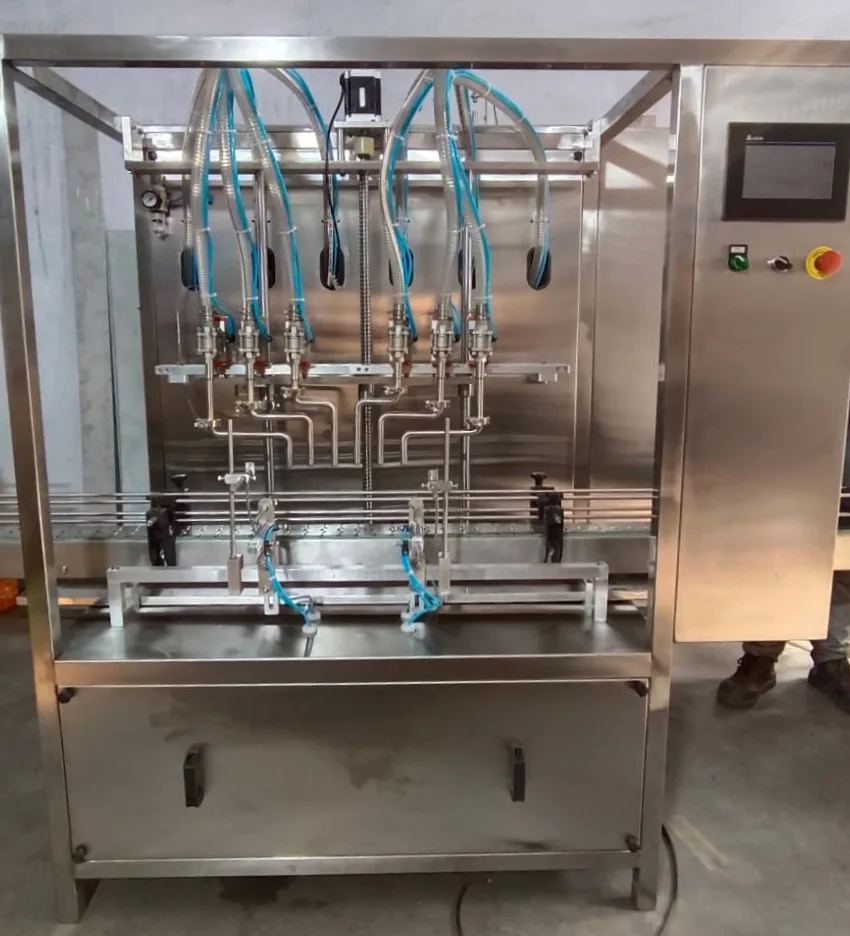
Automatic Oil Filling Machine
Eva Pack Machinery offers a high-performance Oil Filling Machine ideal for edible oil, hair oil, mustard oil, and lubricants. Engineered with advanced automation, it ensures accurate, drip-free filling and supports various bottle types and sizes. Available in single to multi-head options, the machine delivers fast, hygienic, and consistent output with minimal maintenance. Its user-friendly control panel and robust stainless steel build make it perfect for food, cosmetic, and chemical industries. Trusted across India, Eva Pack’s oil filling machines are known for precision, durability, and efficiency—ensuring top performance and better production output for growing businesses.
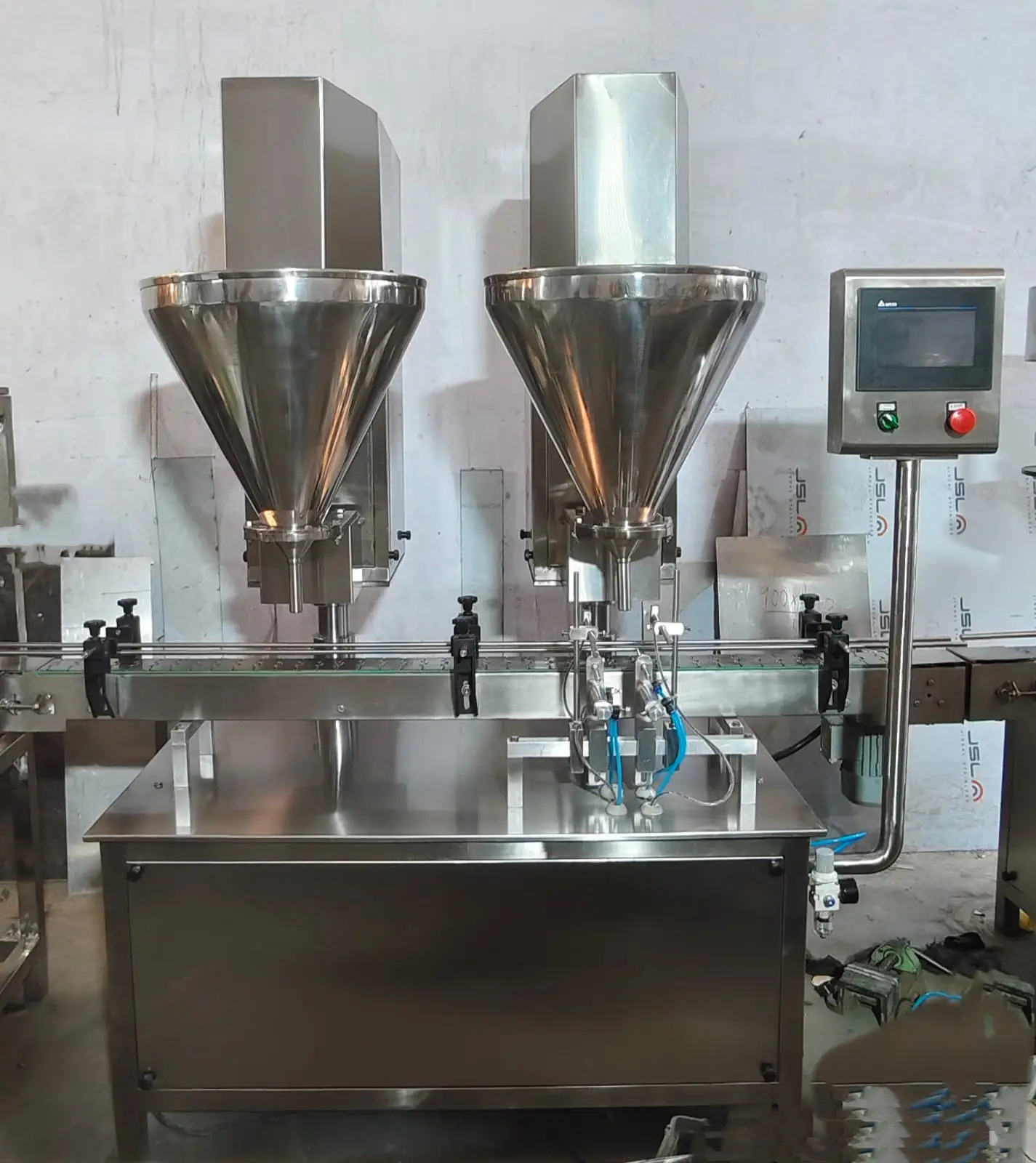
Automatic Powder filling machine
Eva Pack Machinery offers a high-precision Automatic Powder Filling Machine designed for accurate and efficient filling of dry powders like spices, flour, milk powder, pharmaceutical, and chemical powders. Built with advanced servo control technology and a stainless steel body, it ensures consistent filling with minimal wastage. Ideal for bottles, jars, or pouches, the machine supports various filling volumes and is easy to operate and clean. With high speed and precision, it meets GMP standards and is perfect for food, pharma, and chemical industries. Trusted across India, Eva Pack delivers reliable automation solutions for your powder packaging needs.
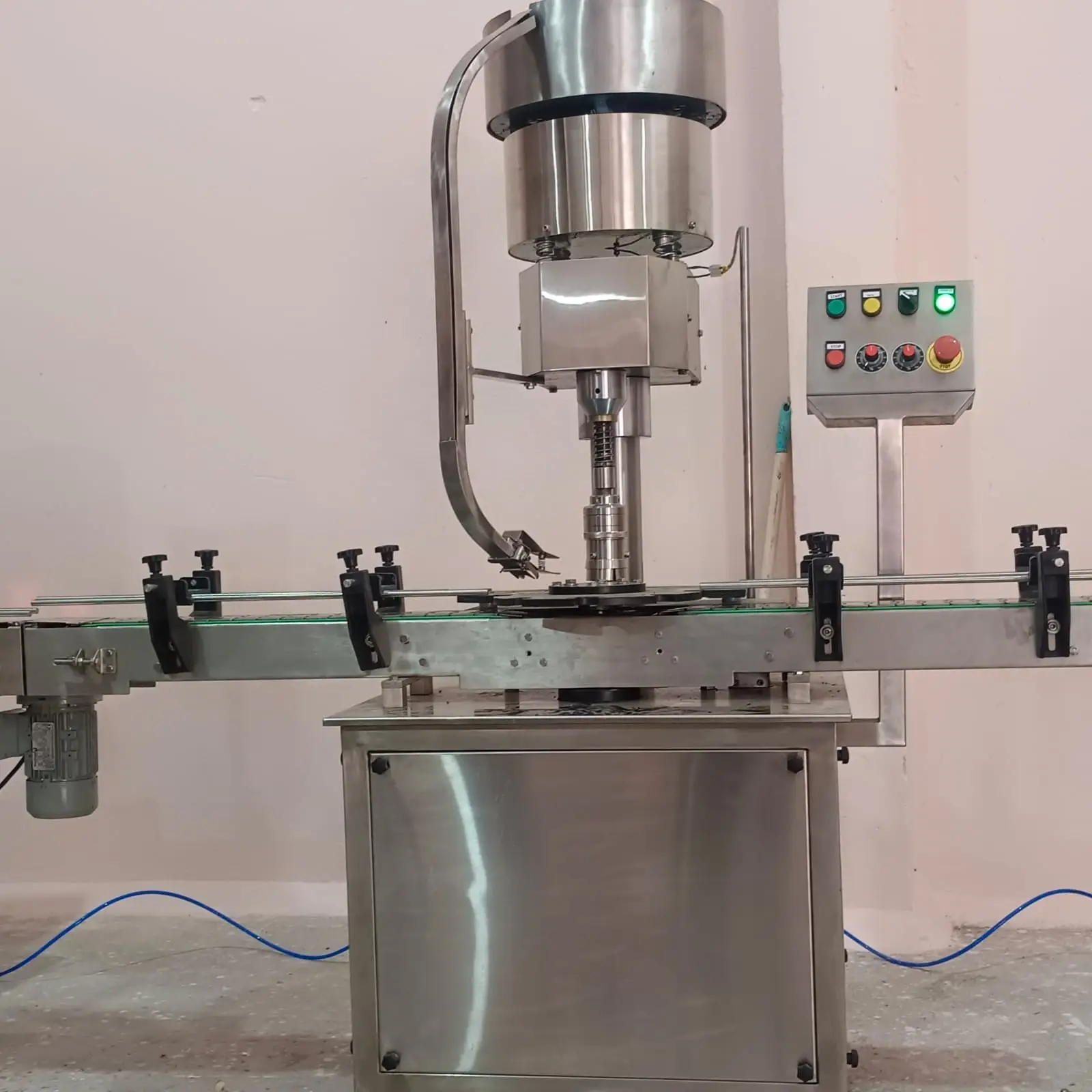
Automatic Bottle Capping Machine
Eva Pack Machinery presents a robust and reliable Automatic Bottle Capping Machine designed for sealing bottles with precision and speed. Suitable for plastic, glass, and PET bottles, it efficiently handles screw caps, ROPP caps, and flip-top caps. Engineered with a stainless steel frame and advanced torque control, it ensures leak-proof, tamper-proof sealing. Ideal for food, cosmetic, pharmaceutical, and chemical industries, the machine integrates smoothly with filling lines. With user-friendly controls, low maintenance, and high output capacity, Eva Pack’s capping machine is the perfect solution for automation-driven production.
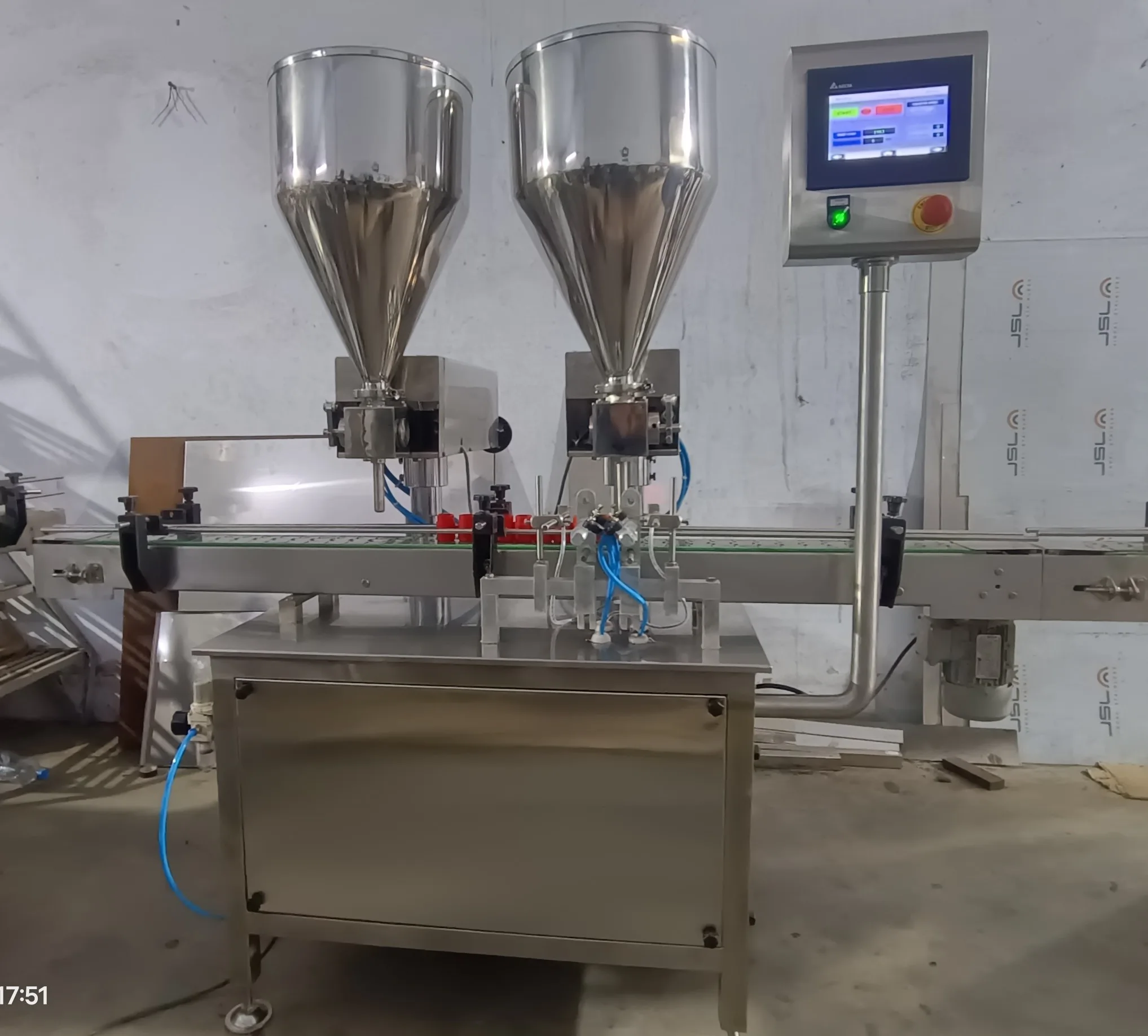
Automatic Cream/Paste Filling Machine
Eva Pack Machinery offers a high-performance Automatic Cream/Paste Filling Machine designed for accurate and hygienic filling of viscous products like creams, lotions, gels, pastes, sauces, and adhesives. Built with a stainless steel structure and servo or pneumatic piston technology, it ensures smooth, drip-free, and consistent filling. Ideal for cosmetic, pharmaceutical, food, and chemical industries, the machine supports various container types and volumes. Its user-friendly touchscreen panel, quick changeover design, and GMP compliance make it a top choice for high-speed production. Eva Pack is a trusted name in filling solutions across India.
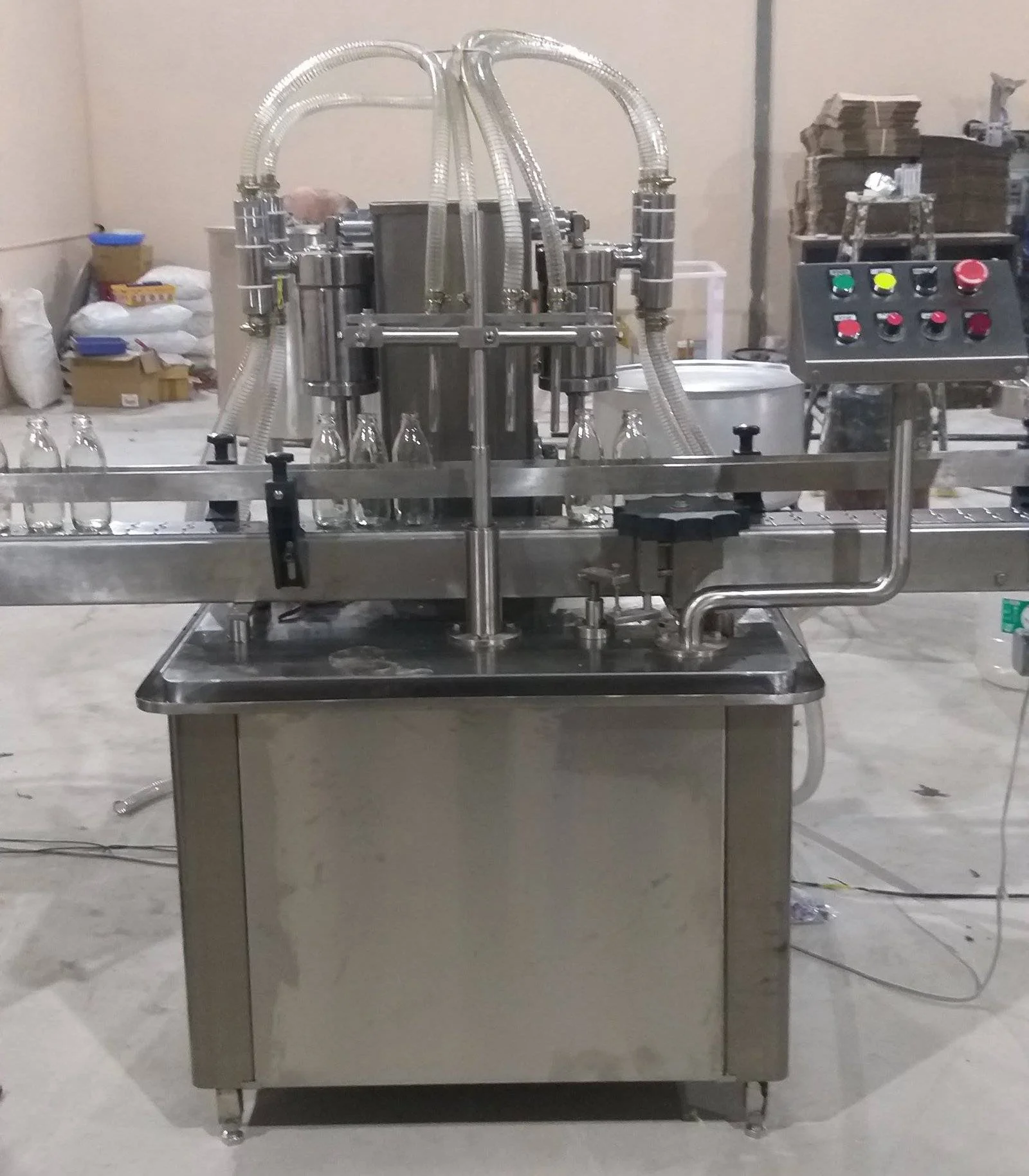
Volumetric Liquid Bottle Filling Machine
Eva Pack Machinery’s Volumetric Liquid Bottle Filling Machine is engineered for precise and efficient filling of free-flowing liquids like juices, syrups, milk, and chemicals. Ideal for small to medium-scale production, it uses piston-based volumetric technology to ensure accurate fills with minimal wastage. The machine supports various bottle sizes and materials, including PET, glass, and HDPE. Built with a stainless steel body, it offers durability, easy cleaning, and user-friendly operation. Suitable for food, pharmaceutical, and cosmetic industries, this machine is perfect for businesses seeking consistency and speed. Eva Pack is a trusted name in liquid filling solutions across India..

Ayurvedic Powder Filling Machine
Eva Pack Machinery offers a precision-engineered Ayurvedic Powder Filling Machine ideal for filling herbal powders, churnas, and medicinal blends into bottles, jars, or pouches. Designed with servo-based auger technology, it ensures accurate, hygienic, and dust-free filling. Built using GMP-compliant stainless steel, the machine is suitable for Ayurvedic, pharmaceutical, and nutraceutical industries. It supports a wide range of filling volumes and container types, with easy-to-use controls and quick changeover features. Trusted by top Ayurvedic brands across India, Eva Pack’s machine delivers efficiency, consistency, and clean packaging for powder-based health products.
Our Product :

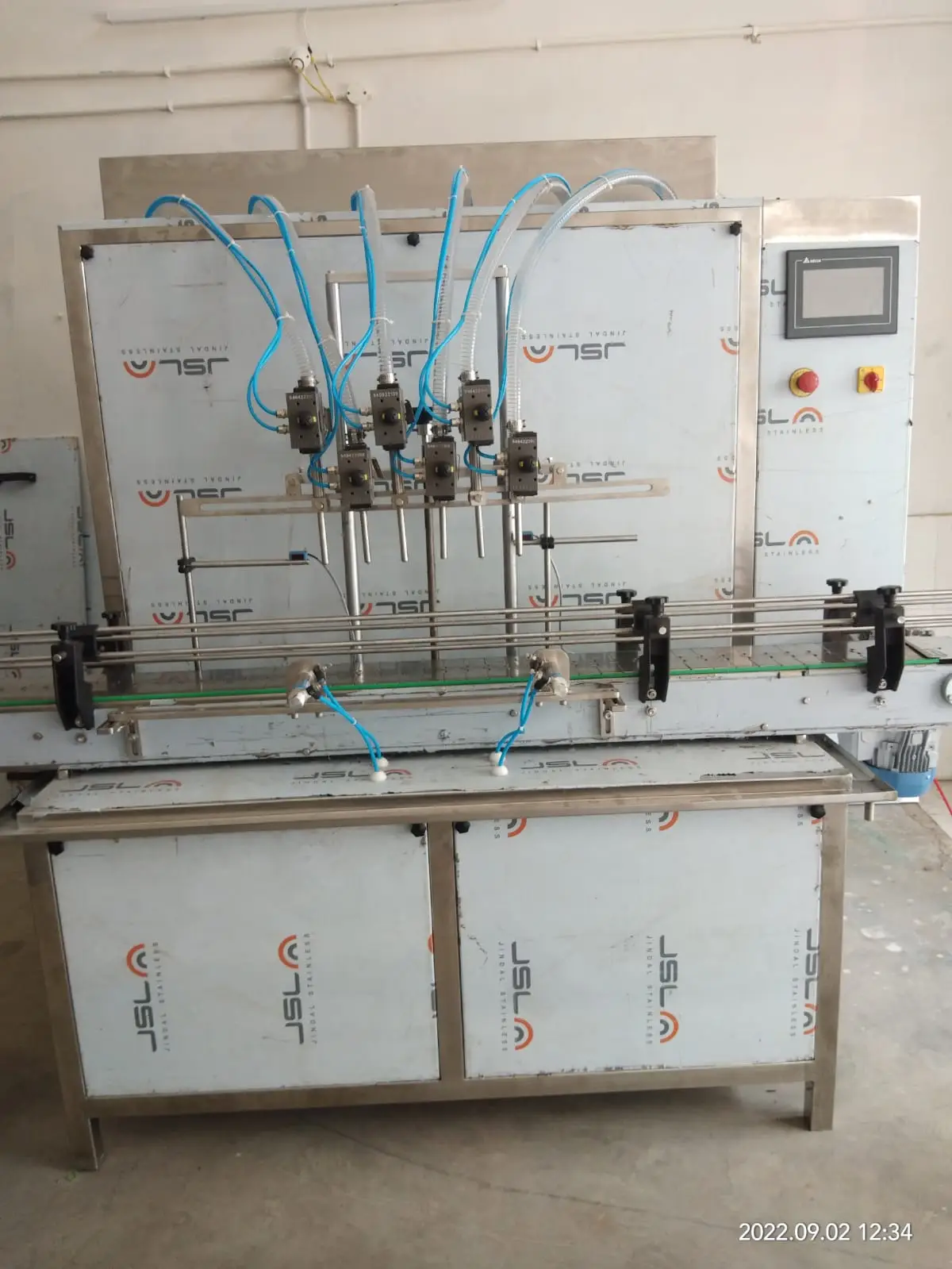


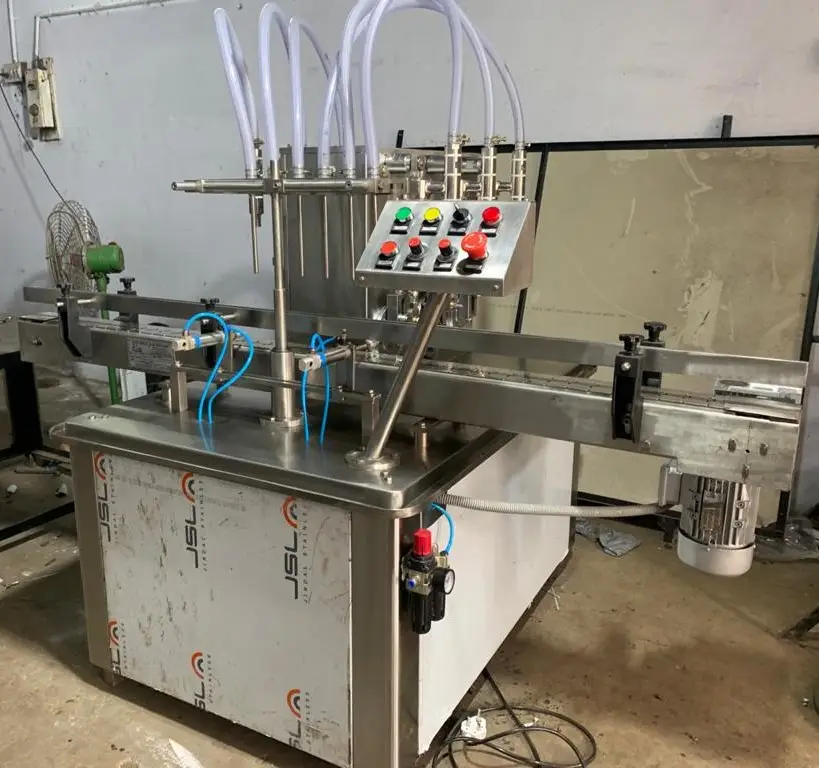
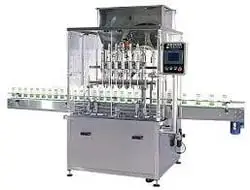

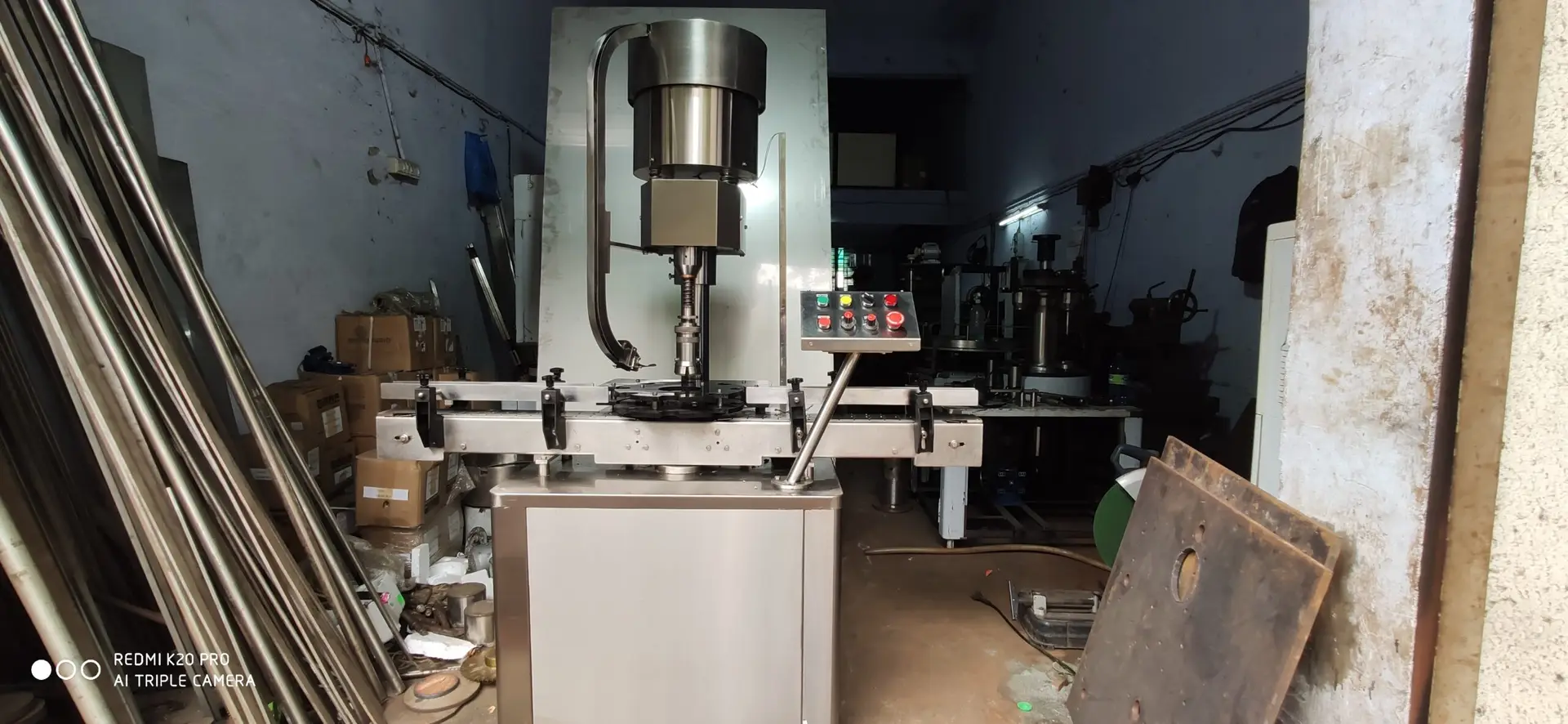
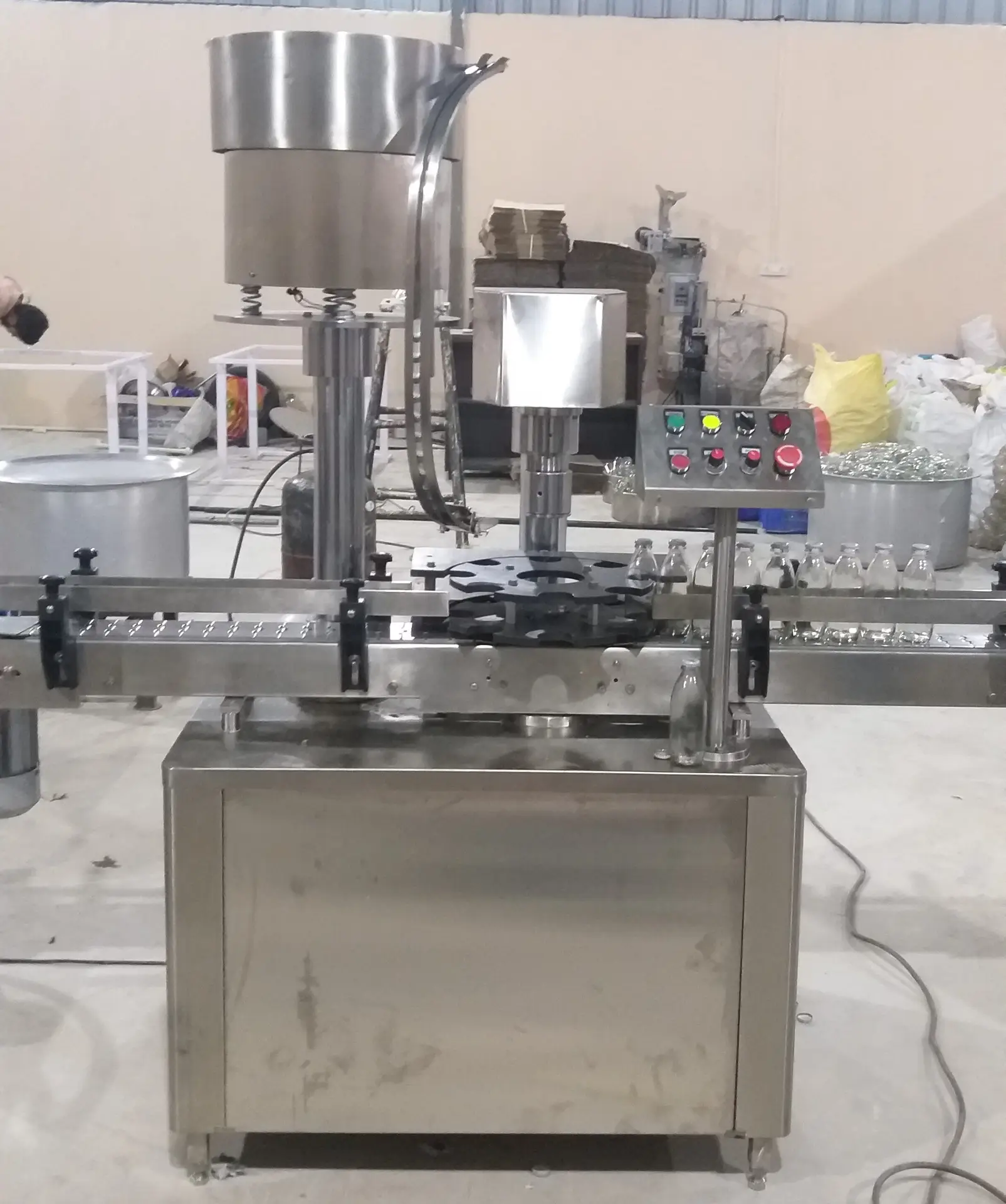
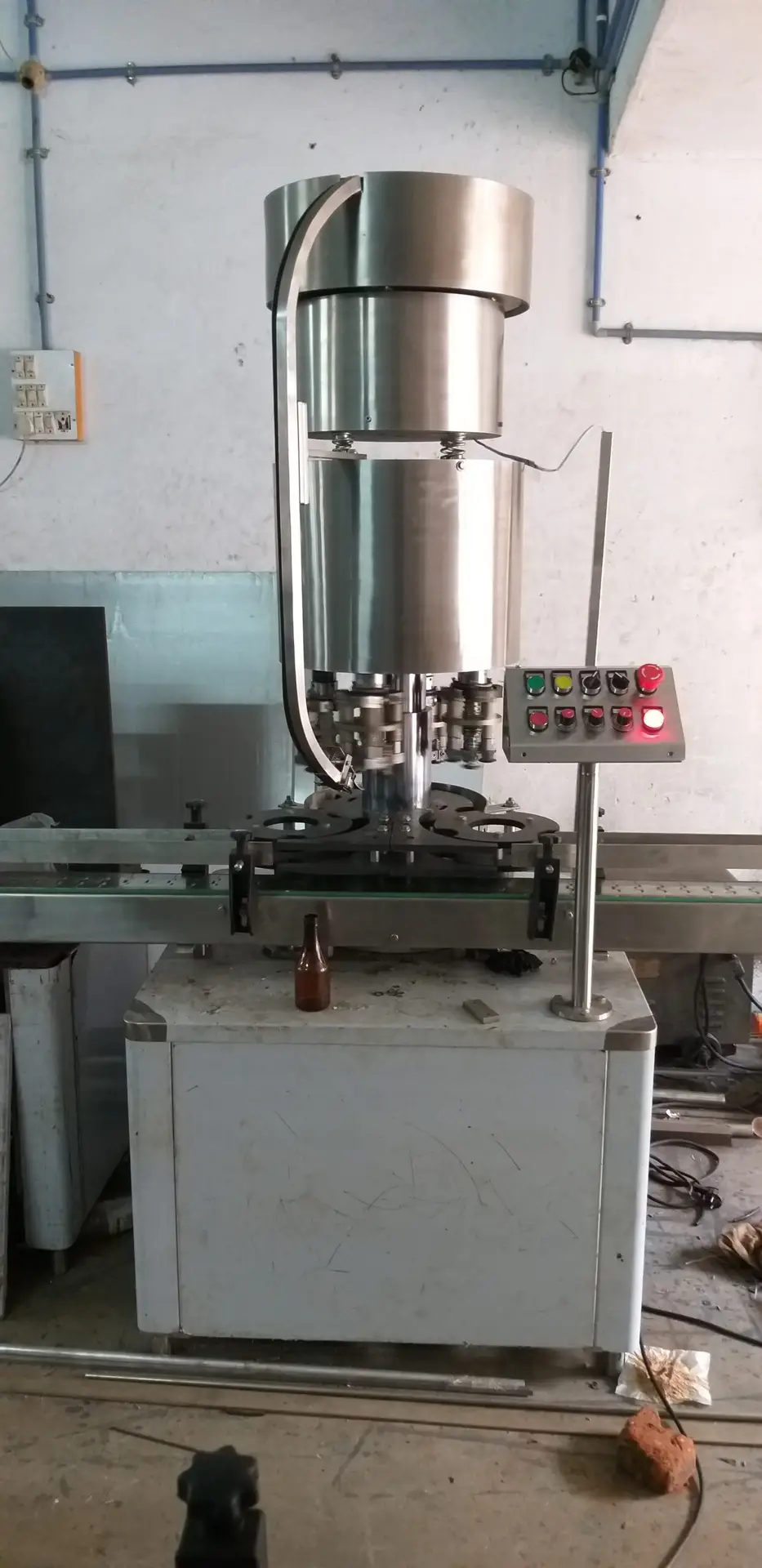
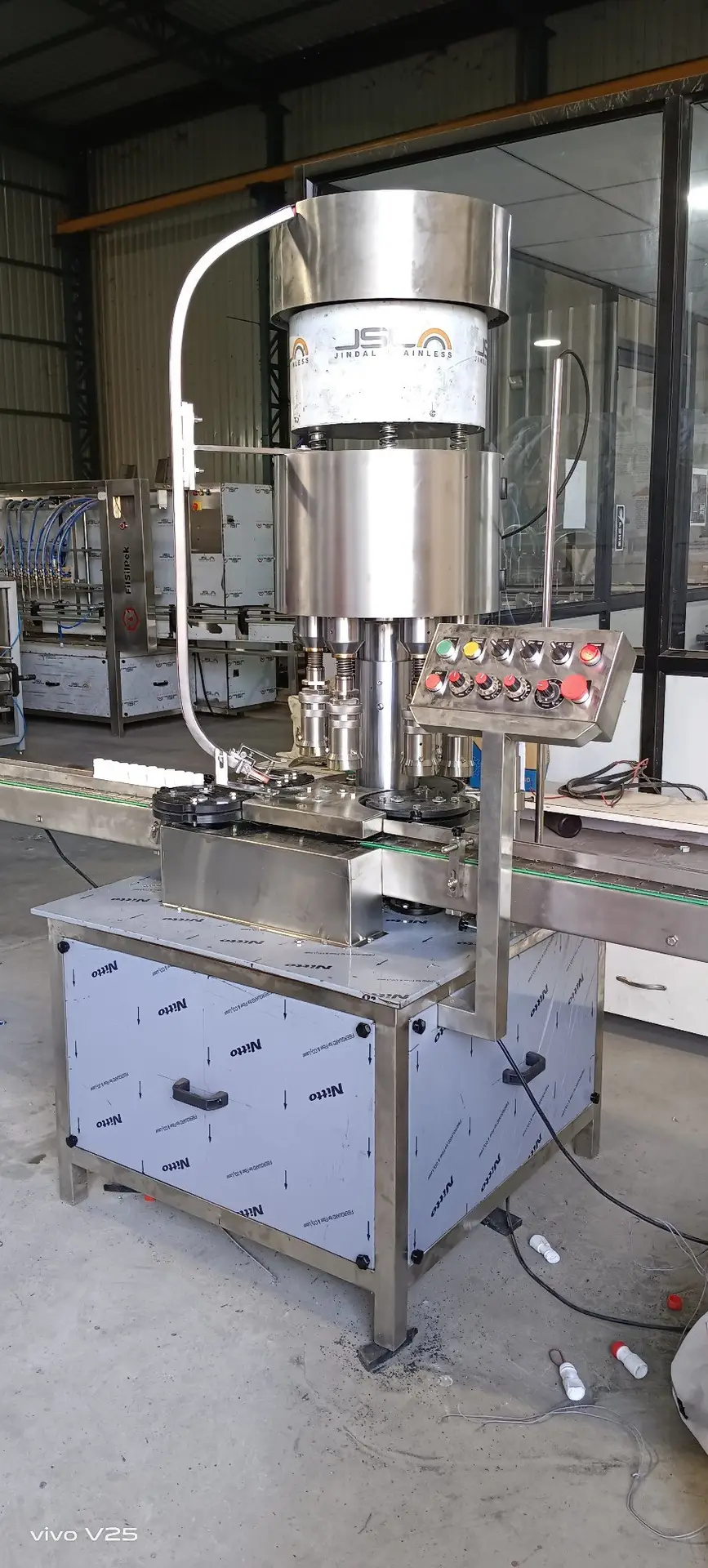
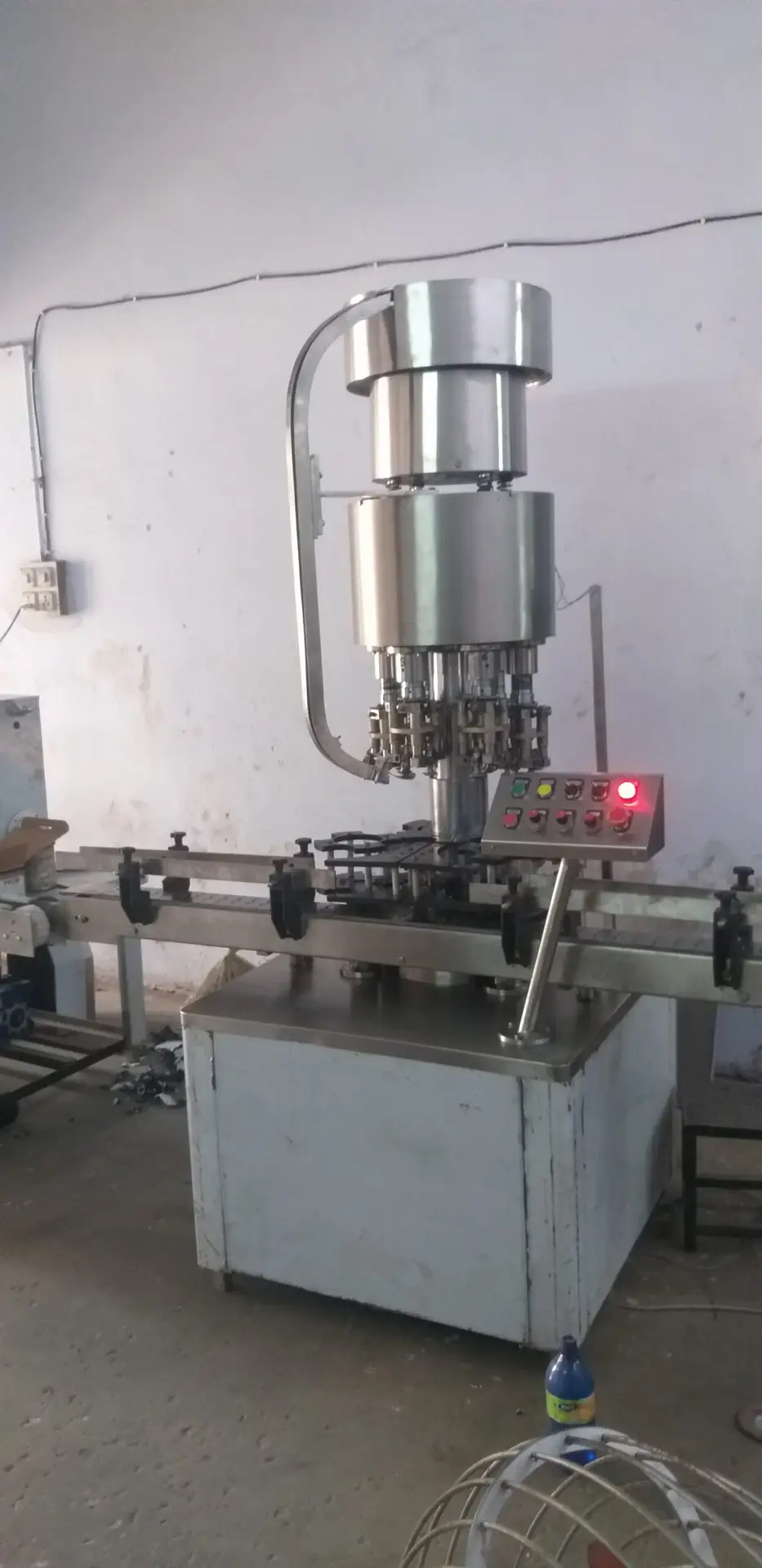
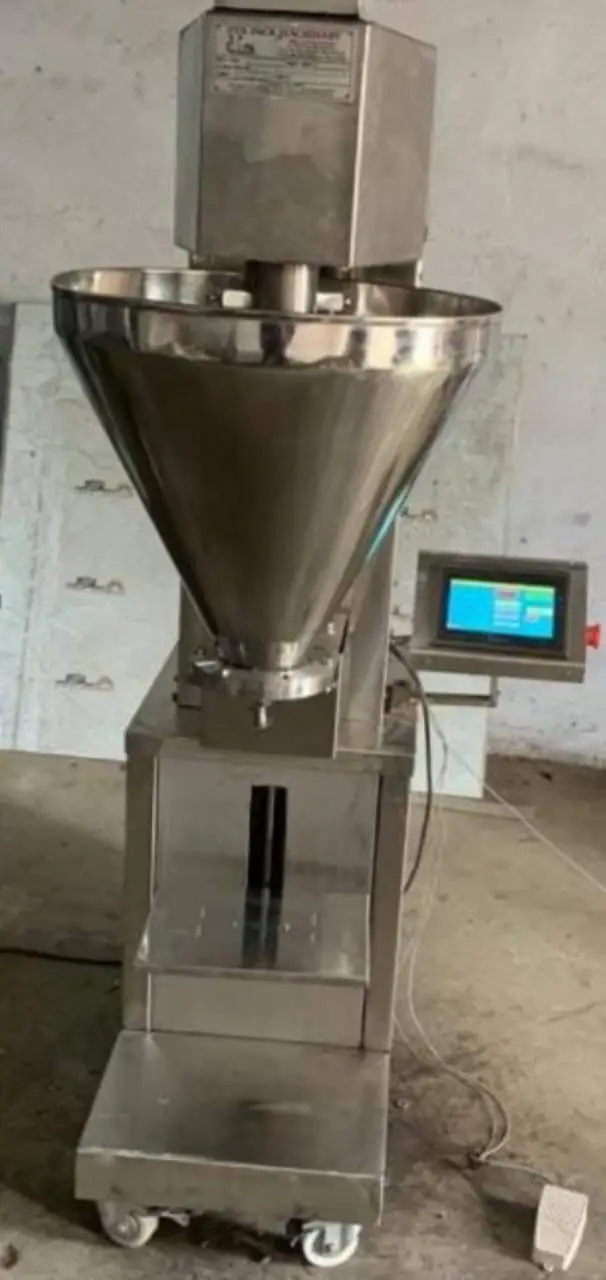
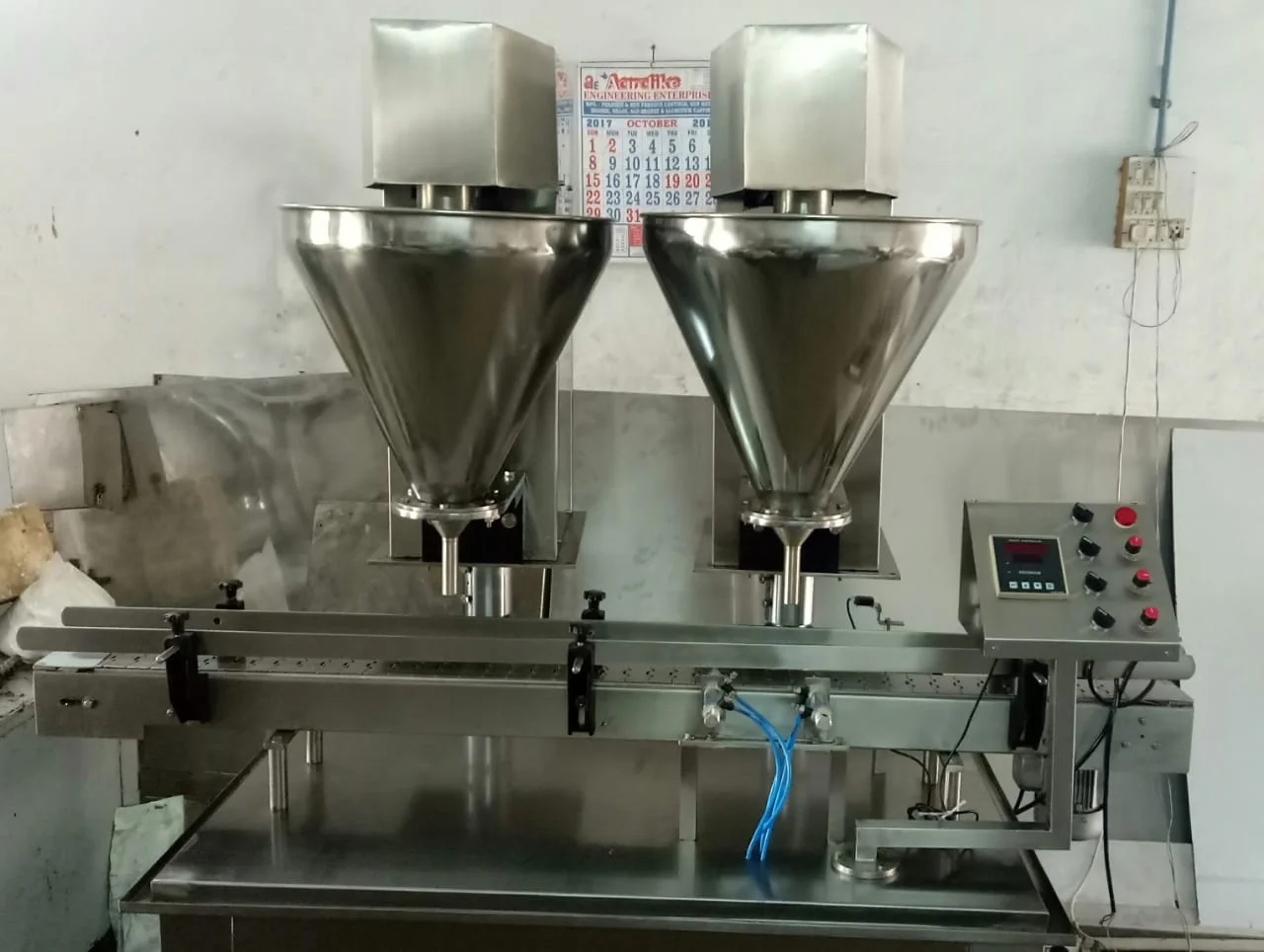
