
TRENDING
A Plastic Bottles Screw Capping Machine is a type of packaging machinery designed to automate the process of screw capping plastic bottles. This machine is commonly used in industries such as beverage manufacturing, pharmaceuticals, cosmetics, and other sectors that require efficient and precise bottle sealing.
Here is a general description of the components and functionalities you might find in a typical Plastic Bottles Screw Capping Machine:
1. **Conveyor System:** The machine usually includes a conveyor system that transports the plastic bottles to the capping station. This conveyor ensures a continuous and orderly flow of bottles through the capping process.
2. **Capping Head(s):** The capping head is the part of the machine responsible for applying the screw caps to the bottles. The number of capping heads depends on the machine’s design and capacity. The heads are designed to securely and consistently screw the caps onto the bottles.
3. **Cap Feeder:** A cap feeder is integrated into the system to supply a steady stream of caps to the capping heads. This can be a hopper or a different feeding mechanism depending on the specific design.
4. **Adjustable Mechanisms:** The machine often has adjustable features to accommodate various bottle sizes and cap types. This includes adjustments for different bottle heights and cap diameters.
5. **Torque Control:** To ensure proper sealing, the capping machine may have torque control mechanisms. These mechanisms allow for the adjustment of the torque applied to the caps, ensuring a tight and secure seal without damaging the bottle or the cap.
6. **Sensor Systems:** Sensors are used to detect the presence of bottles and caps, ensuring that the capping process is initiated only when a bottle is in position.
7. **Control Panel:** The machine is typically equipped with a control panel that allows operators to set parameters such as cap torque, speed, and other relevant settings. It may also include a user interface for monitoring the machine’s performance.
8. **Frame and Enclosure:** The machine is constructed with a sturdy frame to support its components and an enclosure for safety and to prevent contamination of the capping process.
9. **Safety Features:** Depending on the design and regulatory requirements, safety features such as emergency stop buttons and safety guards may be incorporated.
10. **Automatic Cap Sorter (Optional):** In some cases, a capping machine may include an automatic cap sorter that orients the caps in the correct position before they are applied to the bottles.
1. General Specifications
- Machine Type: Automatic Screw Capping Machine
- Model: [EPMCP40, if applicable]
- Construction: Stainless steel (SS 304)
2. Performance
- Capping Speed: 30-50 bottles per minute (BPM), adjustable depending on bottle and cap size
- Bottle Diameter Range: 20 mm – 120 mm
- Bottle Height Range: 50 mm – 300 mm
- Cap Diameter Range: 25 mm – 80 mm
3. Dimensions and Weight
- Machine Dimensions: 750 mm (L) x 800 mm (W) x 1500 mm (H)
- Weight: 400 kg (approx.)
4. Power Requirements
- Power Supply: 220V, 50/60 Hz, single-phase (customizable for different regions)
- Power Consumption: 2 kW
5. Control System
- Functions:
- Speed adjustment
- Cap torque control
- Bottle and cap detection
- Error diagnostics
6. Features
- Cap Feeding System: Vibratory bowl feeder or cap elevator
- Cap Placement: Automatic cap placement with servo motor control
- Capping Mechanism: Pneumatic or mechanical chuck system
- Safety Features:
- Emergency stop button
- Safety guards and interlocks
- Bottle Positioning: Star wheel or indexing conveyor system for precise positioning
- No Bottle-No Cap System: Prevents wastage by stopping the machine if no bottle is detected
- Cap Rejection System: Automatically rejects improperly placed caps
7. Materials and Finish
- Machine Frame: SS 304/316
- Contact Parts: FDA-approved materials (e.g., SS 316, food-grade plastic)
- Surface Finish: Mirror finish for hygienic applications
8. Environmental Requirements
- Operating Temperature: 10°C – 40°C
- Humidity: Up to 85% non-condensing
9. Maintenance and Warranty
- Maintenance: Easy access for cleaning and maintenance, tool-less changeover parts
- Warranty: 1 year standard warranty with optional extended warranty
1. Technological Advancements
- IoT Integration: Enhanced connectivity for real-time monitoring, predictive maintenance, and remote troubleshooting.
- AI and Machine Learning: Adaptive algorithms for optimizing capping torque and speed based on bottle and cap variations.
- Automation and Robotics: Improved automation for cap sorting, placement, and sealing, potentially using robotic arms for higher precision.
2. Sustainability Enhancements
- Energy Efficiency: Incorporation of energy-efficient motors and drives, regenerative braking systems.
- Eco-friendly Materials: Use of biodegradable or recyclable materials for parts in contact with consumables.
- Waste Reduction: Advanced systems for minimizing waste during changeovers and operational downtime.
3. Customization and Flexibility
- Modular Design: Easy scalability and customization for different production volumes and cap/bottle types.
- Quick Changeover: Faster and more intuitive changeover processes to accommodate multiple product lines with minimal downtime.
- Smart Cap Detection: Enhanced sensors and vision systems to handle a wide variety of cap shapes and sizes with minimal manual intervention.
4. Regulatory Compliance
- Global Standards: Adherence to increasingly stringent global safety and hygiene standards.
- Data Integrity: Improved data logging and traceability features to meet regulatory requirements for pharmaceutical and food industries.
Related Product:
Our Product
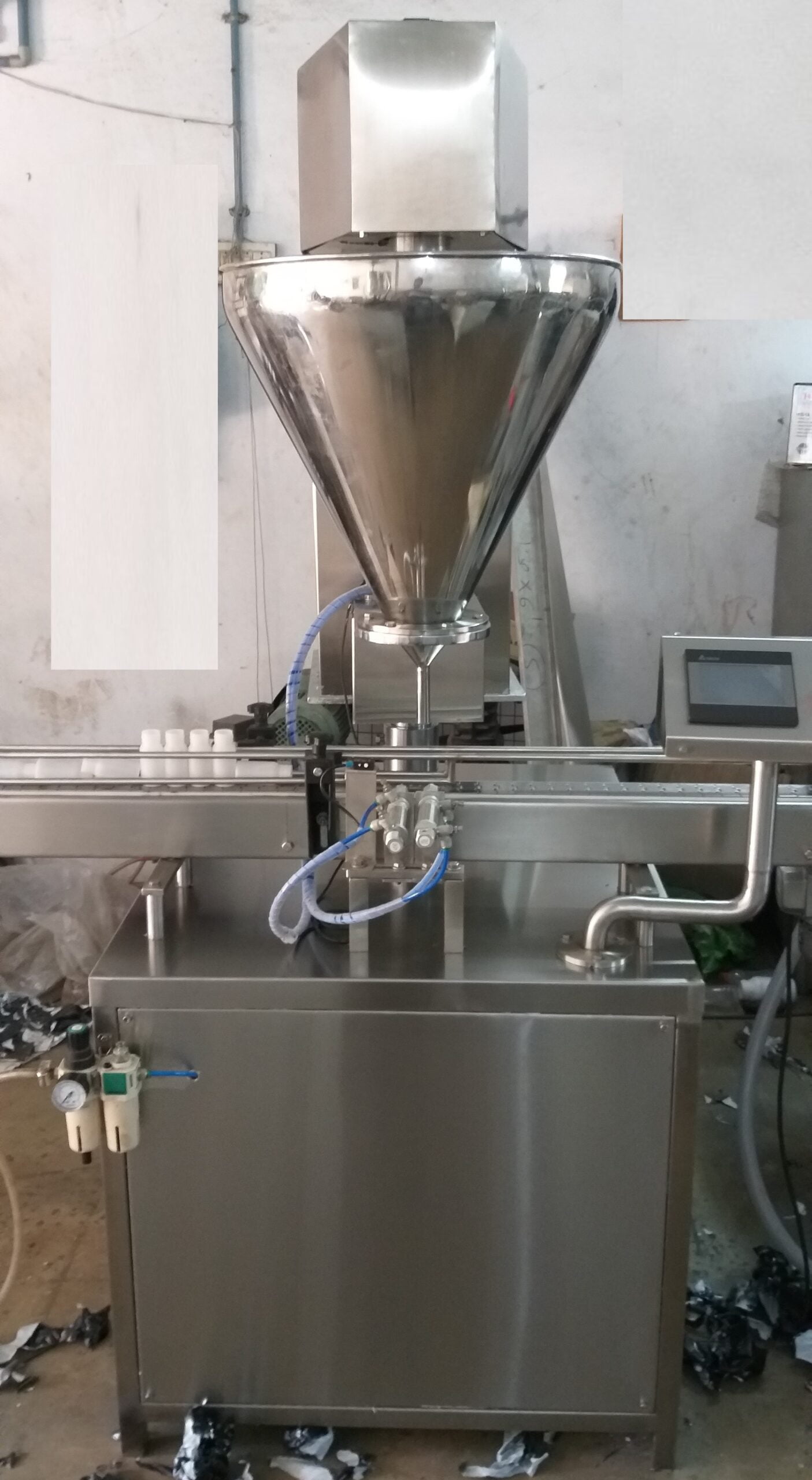
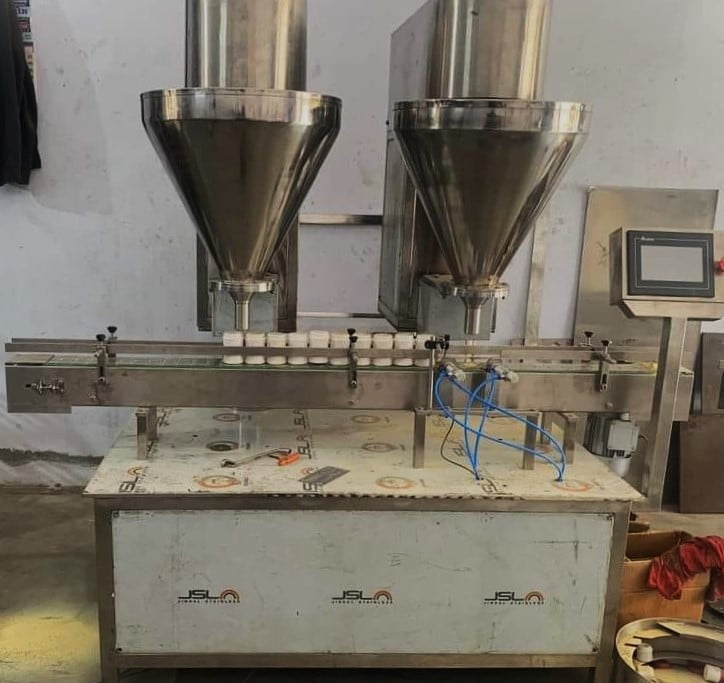
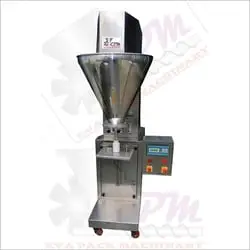
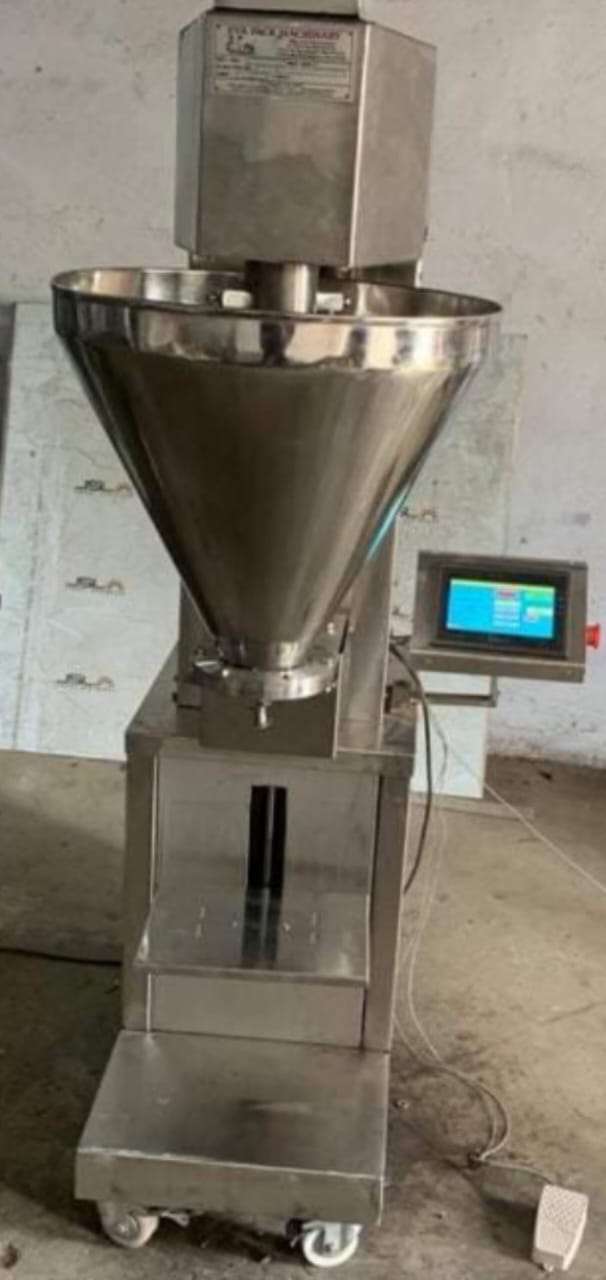
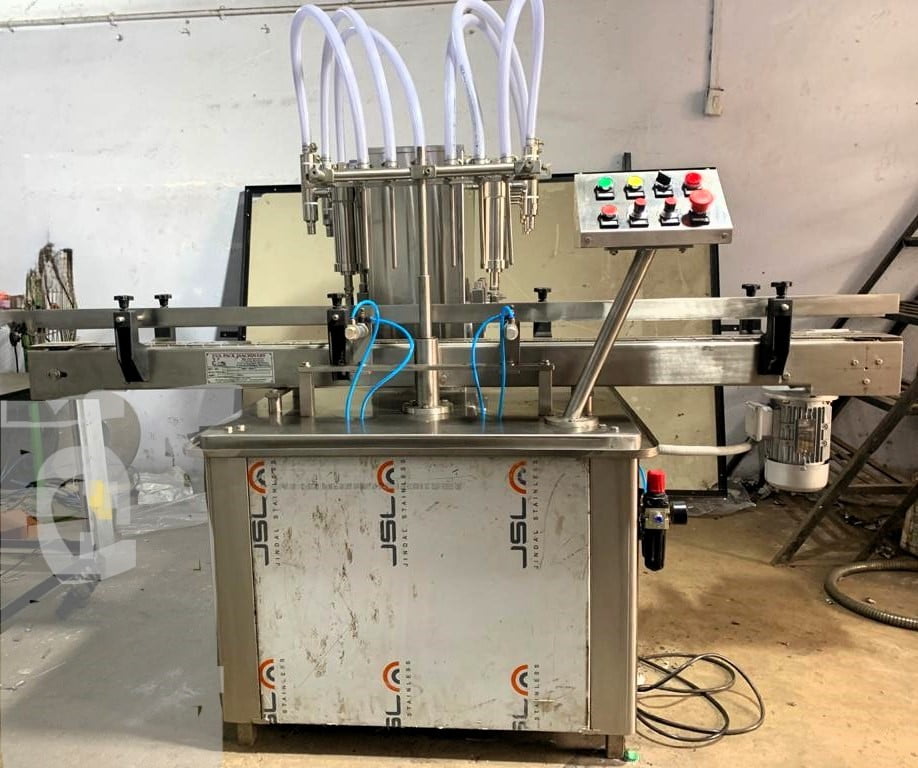
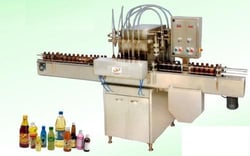
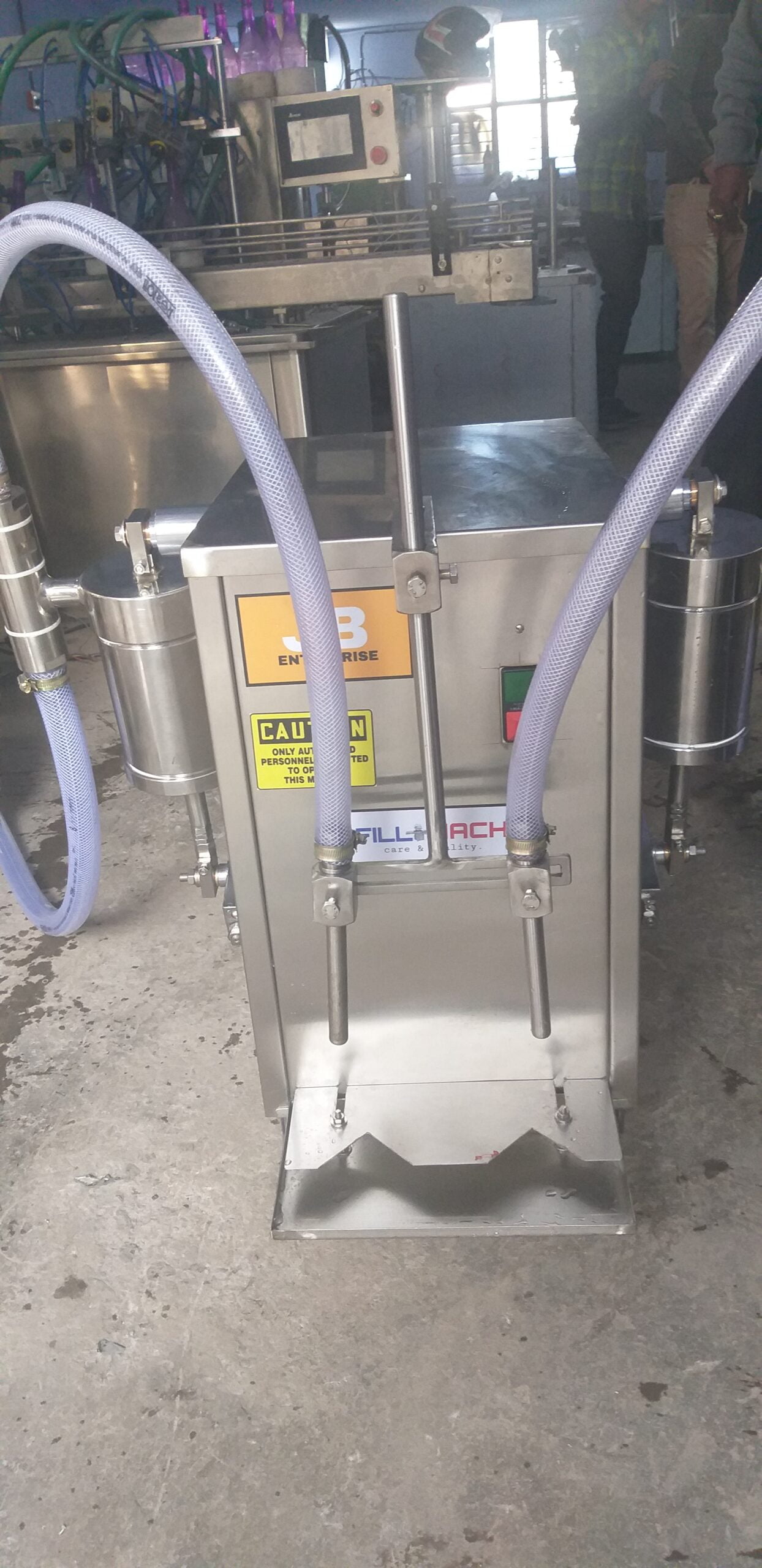
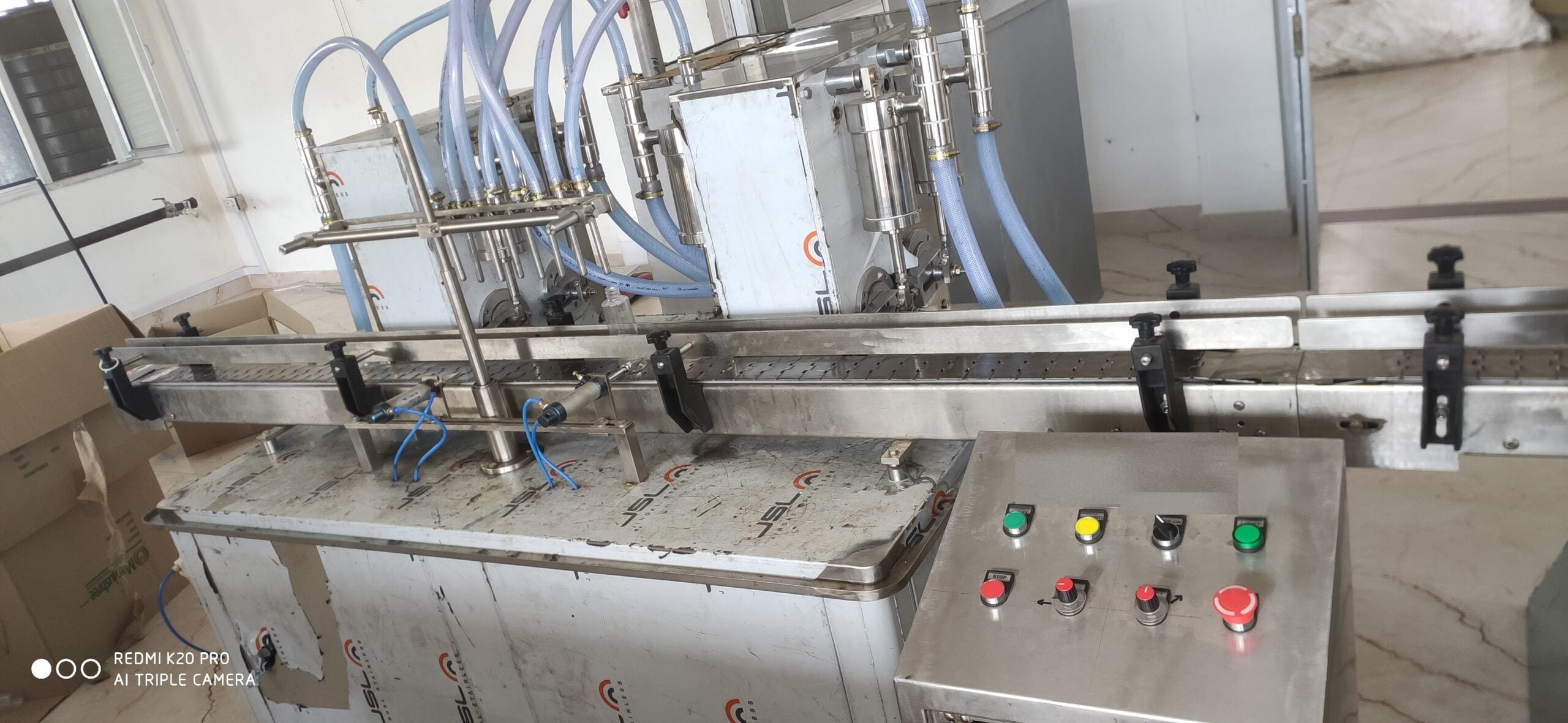
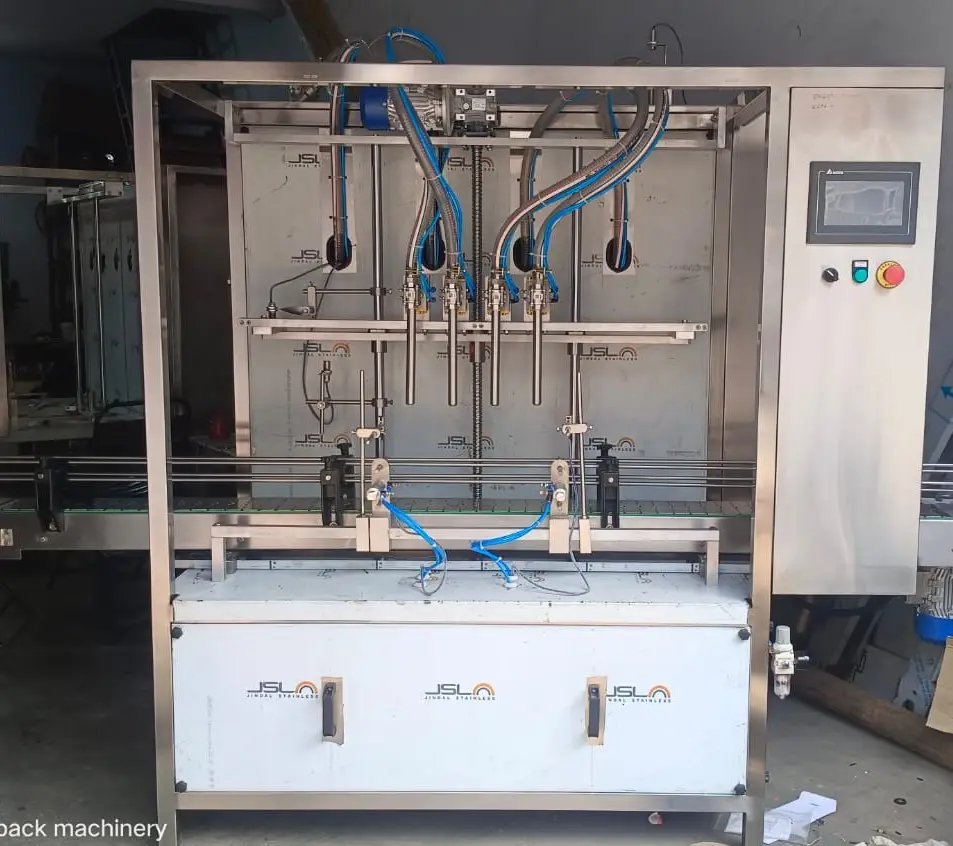
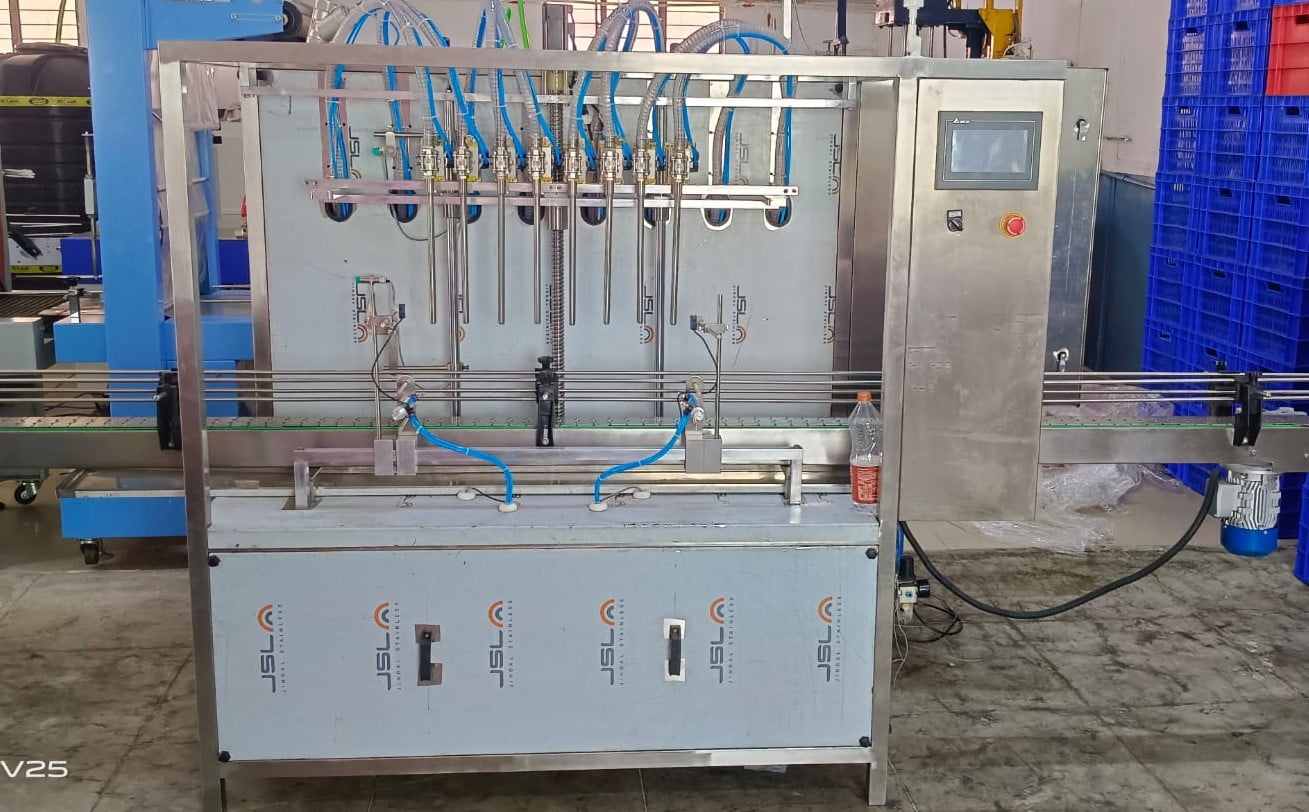
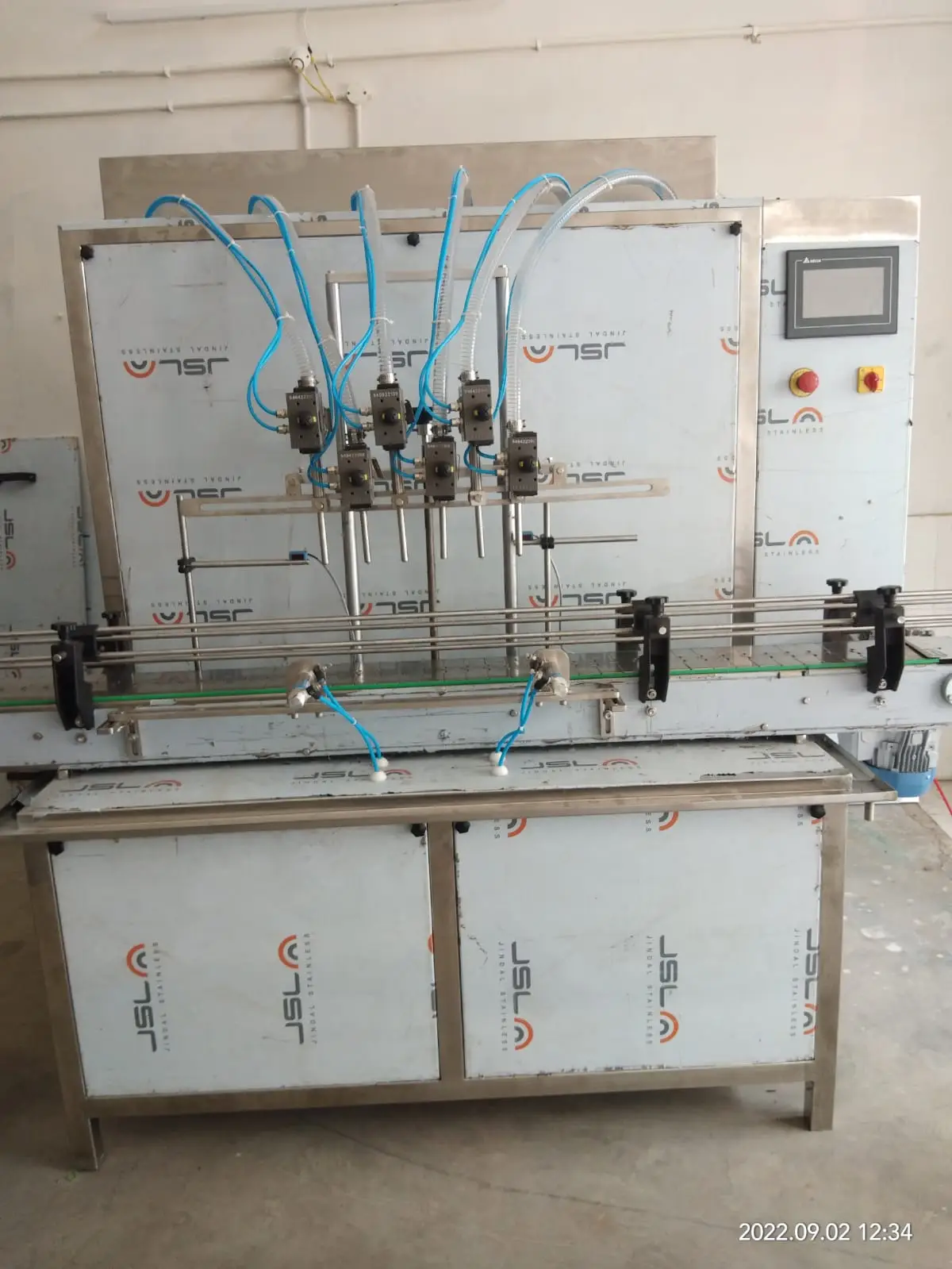
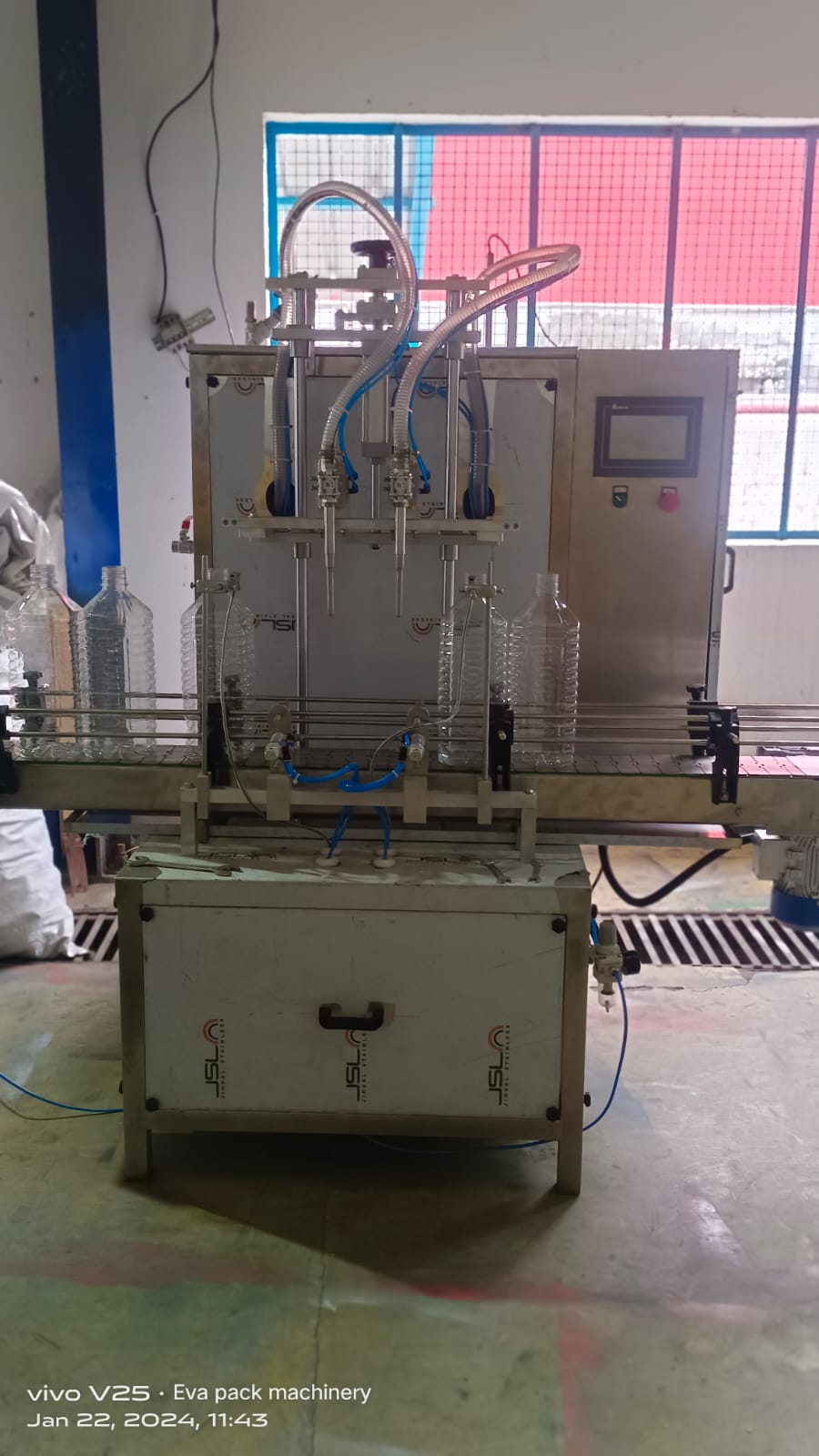
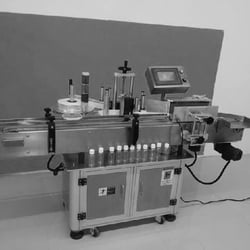